Welcome to Part 2 of our series exploring the main components of ceramic glazes!
As you’ll remember from our previous article, all glazes are composed of 3 main parts: glass-formers, fluxes, and stabilizers. In Part 1 we discussed the oh-so-essential glass-former, silica. This week we’re going to explore an important ingredient that supports those glass-formers: Flux. We have a lot more options to explore in this category — but don’t be overwhelmed! By understanding these materials, you will have a much clearer picture of what is going on in your glazes.
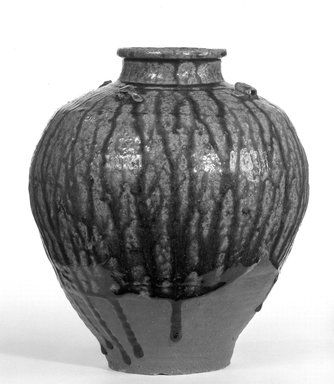
Brooklyn Museum
The Role of Flux
Fluxes are types of oxides that are found in a variety of minerals. The main job of a flux is to help silica, our glass-former, to melt in the kiln. As you may remember, silica has a very high melting point. To help bring that melting point down so we can glaze ceramics at a wide variety of firing temperatures, we add a flux. Often a glaze will have more than one source of flux, and, typically, the more kinds of fluxes present in a mix, the lower its melting temperature.
Fluxes have some secondary effects as well. They promote vitrification, which is what helps our glazes to be water-tight and capable of holding liquids. They can affect the surface quality and opacity of the glaze. And, importantly, they affect the color results of different metallic oxides. Some colors are only possible by combining the right oxide colorant with the right flux!
What Ingredients Provide Flux to Glazes?
There are nine main fluxes that ceramic artists are likely to encounter, as well as some lesser-used ones. They can be lumped into a few distinct groups based on similar fluxing properties. These include things such as melt temperature, thermal expansion, surface characteristics, and color impact. Oxides within a given group generally make better substitutions for each other than oxides from different groupings, while combining oxides from different groups can help offset common defects. Let’s have a closer look at the ones you’re most likely to encounter…
Alkaline Earth
This group contains oxides that melt at medium-high temperatures. They are moderate fluxes with relatively low thermal expansion. They are great for promoting matte finishes, though are also capable of producing gloss. This group includes:
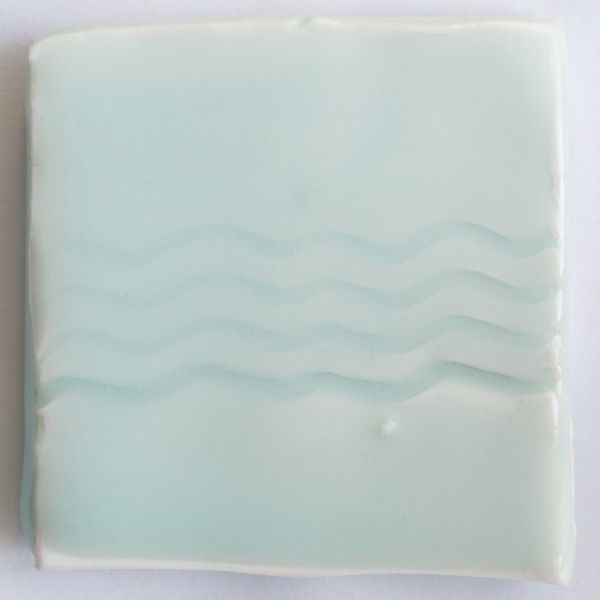
sourced from wollastonite
Calcium Oxide (CaO)
This is a primary flux in many mid-high firing glaze recipes, with its melting action beginning around 2012F (1100C). It’s not particularly effective in glazes below cone 4, but you may see it in lowfire lead glazes where it acts more as a melt assistant, rather than the main player.
In high amounts, CaO can lead to crystallization, making it useful for matte glazes. It also has excellent color responses.
CaO does not occur in pure form naturally, so we have to source it from other minerals. To add CaO to our glazes, we use materials such as whiting (calcium carbonate), dolomite (magnesium carbonate), and wollastonite (a calcium inosilicate, CaSiO3).
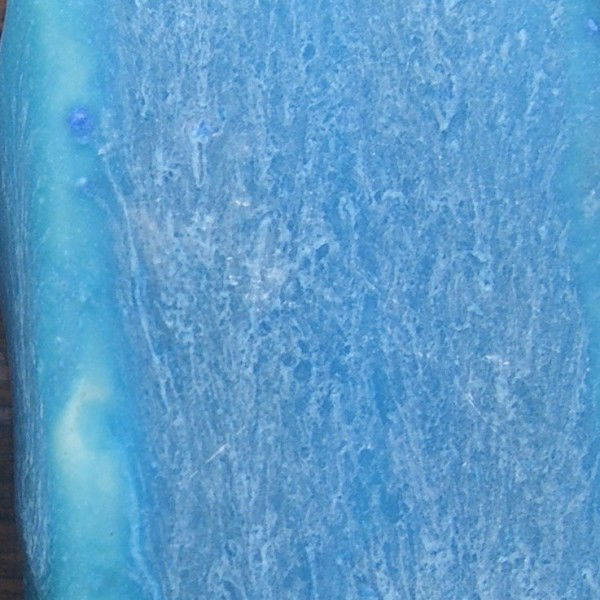
Barium Oxide (BaO)
As you can predict by its placement in the alkaline earth group, BaO is not suitable for lower temperature glazes, being much better suited for high firings. It is best known for its ability to promote unique colors, such as the famous ‘barium blue’. It’s great for producing matte finishes, and is only required in small amounts to produce a good melt. Its finished surface is not quite as hard as that of CaO.
Caution must be taken when using this oxide on functional ware. It’s highly toxic and if fired incorrectly it’s leachable, presenting a notable health hazard. For this reason, unless you are after the unique color or surface properties of this material for decorative works, it’s better to opt for another oxide in this group that does not have the same risks. It’s particularly toxic in its powder form, so use extra caution when preparing your glaze.
Barium oxide is sourced from barium carbonate, or in a slightly safer form in frits, such as Fusion Frit F-403.
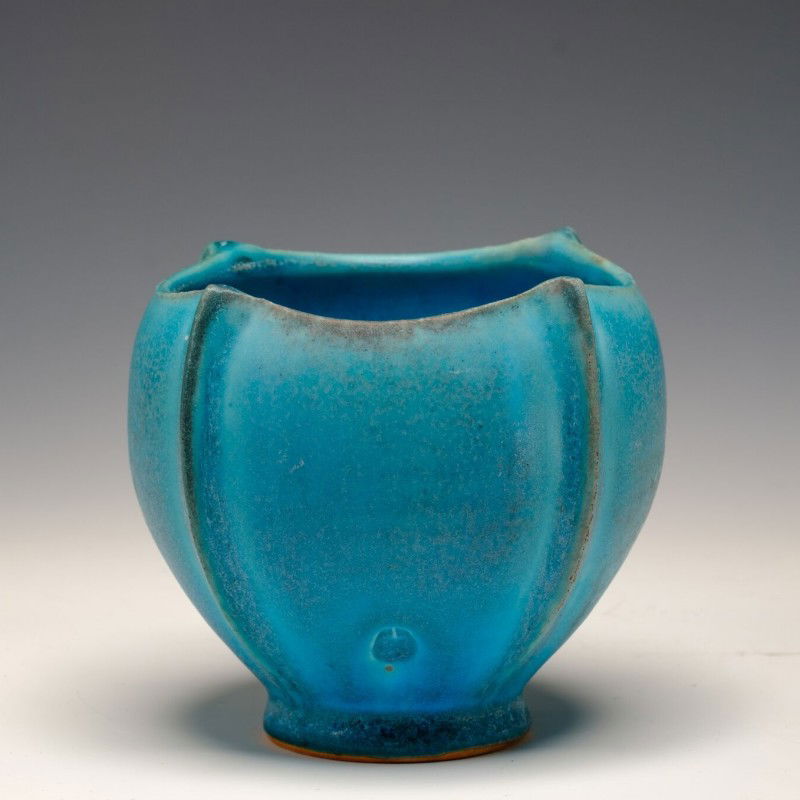
Notice how similar it is to the barium example
Strontium Oxide (SrO)
Similar to the others in this group, SrO has a high melting point (starting around 2012F/1100C). It is an excellent replacement for BaO, being much safer, with similar matte qualities. It is a bit more powerful as a flux than barium, so less is needed. It can also be used in tandem with CaO to produce a clearer gloss, and added in small amounts to low temperature glazes to help the primary fluxes. It is capable of supporting vibrant colors.
To add strontium oxide to your glaze, you can use strontium carbonate, or frits such as Fusion Frit 581.
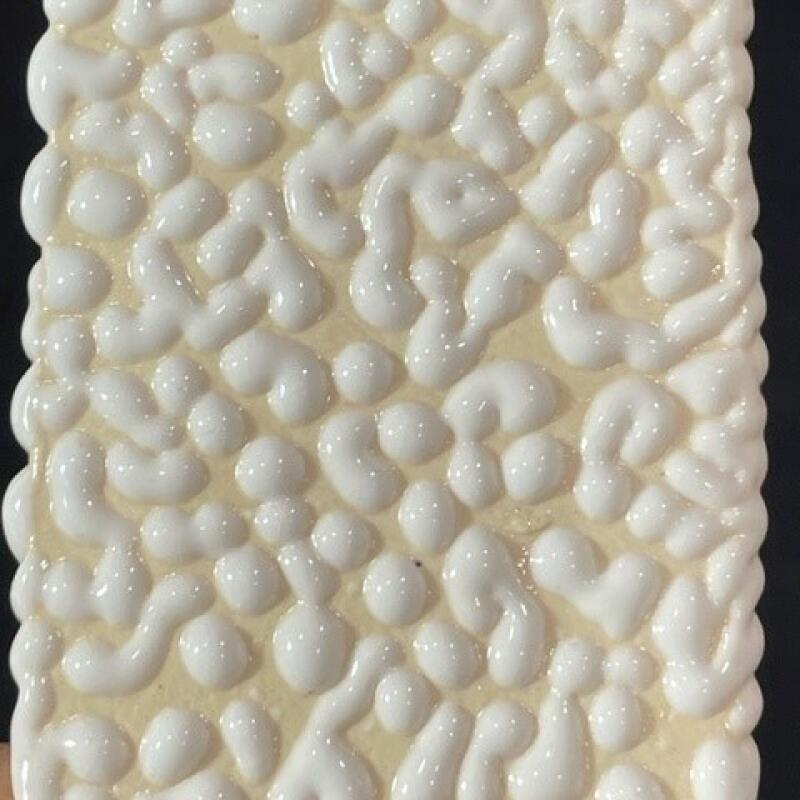
Magnesium Oxide (MgO)
This is the highest melting oxide, fluxing at 5072F (2800C), though it can surprisingly be used to help the fluxing action in even low temperature glazes. It is fantastic for producing matte finishes, with greater amounts increasing the effect without impeding the melt. With its low rate of thermal expansion, it’s useful for reducing crazing.
MgO is great for producing purples, pinks, and lavenders from cobalt, though it’s not the best choice for producing vibrant colors from other metallic oxides. It also has an opacifying effect at lower temperatures, and at high amounts it is used to create the characteristic crawling effects of lichen glazes.
Magnesium oxide is most commonly sourced from talc (magnesium silicate), dolomite (calcium magnesium carbonate), magnesium carbonate, and various feldspars and frits, including Ferro Frit 3249.
Alkali
Fluxes in this group are stronger than Alkaline Earths. They have a higher thermal expansion and broad melting range. They are known for promoting intense colors and glossy surfaces.
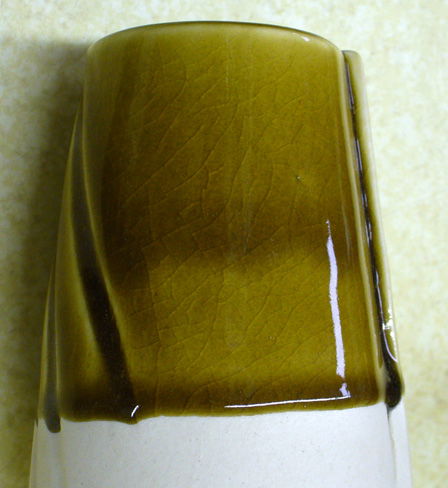
rich color, and crazing defect
Sodium Oxide (Na2O)
Also referred to as Soda, Na2O is the strongest common flux and works from 1650-2370F (900-1300C). Operating very similarly to potassium oxide (K2O), you may see the two lumped together as KNaO.
In addition to its broad melting range, Na2O is used for its ability to promote bright, clear colors, particularly when paired with copper, cobalt, or iron.
On the downside, sodium oxide has a high rate of expansion that leads to significant crazing in glazes where high amounts are present. It can also produce glazes which are softer and less resistant to wear. These potential defects can be offset by substituting some of the Na2O with another oxide.
Na2O is most often sourced from soda feldspars and frits, such as Minspar 200, Frit F3110, and nepheline syenite. In the case of soda firing, where the oxide is added to the kiln during firing, the Na2O is sourced from sodium carbonate (soda ash) or sodium bicarbonate (baking soda).
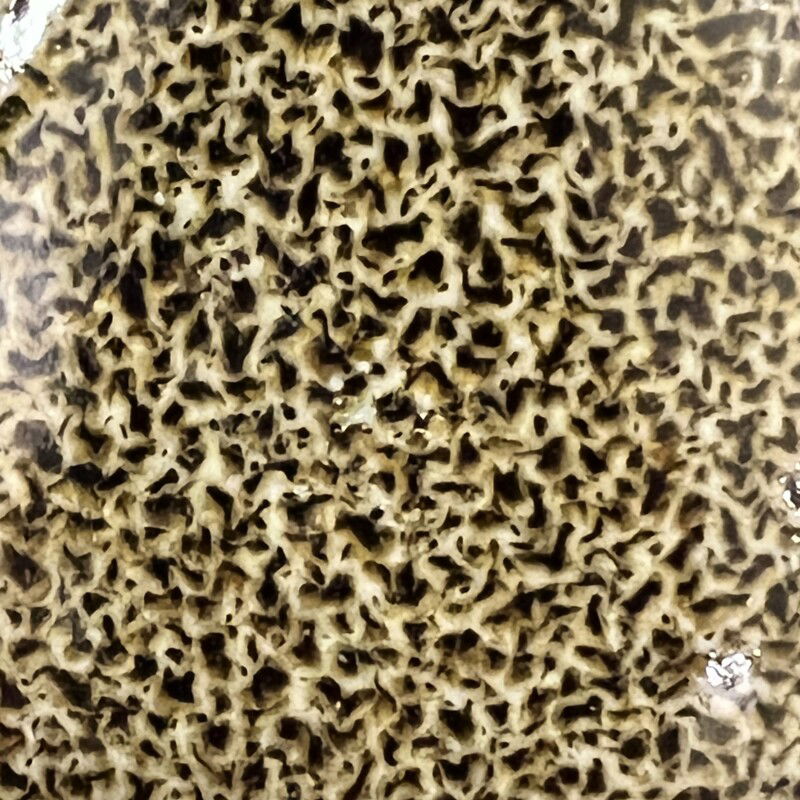
Potassium Oxide (K2O)
As we mentioned above, K2O behaves very similarly to sodium oxide. So why would you choose potassium over soda? Well, it promotes greater melt viscosity than its sodium counterpart, meaning it will result in more fluid glaze effects. It also allows some of the brightest colors of all fluxes (except for lead). And lastly, it can produce a more brilliant glossy glaze over a longer firing range.
Potassium oxide has a similar drawback to sodium, in that it can promote crazing, and has a soft surface.
Like sodium oxide, it’s sources from various feldspars and frits. You may also see it referred to as Potash.
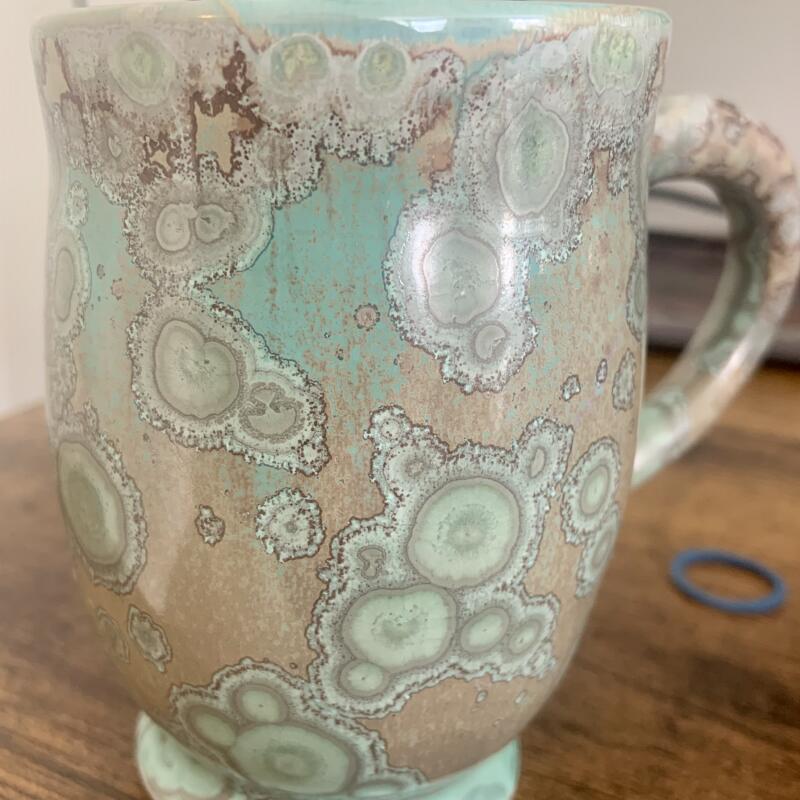
Lithium Oxide (Li2O)
Another alkali oxide, lithium acts much like sodium and potassium, but with the benefit of having a lower thermal expansion. As the most reactive of the fluxes, it’s only used in small amounts, and is great for offsetting the crazing that occurs with the other two alkali oxides. It begins to soften around 1333F (723C).
1% additions can increase glaze gloss noticeably, and slightly greater amounts (3%) can reduce the melting temperature by several cones. It is excellent at promoting colors, particularly blues, and can be used to create a variegated color effect as well. Using it in too high amounts will result in shivering (the glaze flaking off the pot) and excessive flow.
Lithium is primarily sourced from lithium carbonate, and it can also be found in petalite, lepidolite, spodumene, and some frits such as Fusion Frit F-493.
Metallic Oxides
As the name implies, these oxides contain metal. Generally speaking, they’re used to supply color to our glazes. However, there are two oxides within this group that are primarily used for their fluxing properties, rather than their color. Let’s have a look:
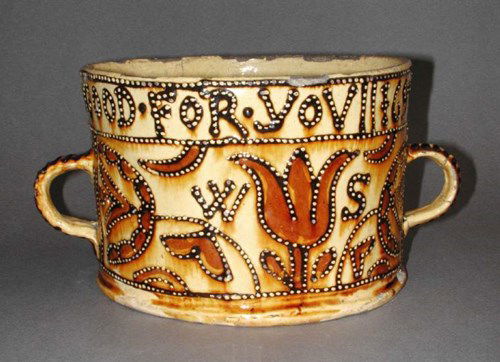
slip-trailed decoration. Fitzwilliam Museum
Lead Oxide (PbO)
Lead oxide became popularized as a flux for its ability to produce a high-gloss, chip-resistant glaze at low firing temperatures. It also famously supports very vibrant colors. It’s a ‘forgiving material’ that tends to hide imperfections on the finished fired surface, and for this reason, is considered easy to use.
Depending on where in the world you’re based, PbO may or may be available for use. It is safe when fired correctly, but it is difficult for the average studio potter to ascertain this with absolute certainty. It is certainly toxic in its raw state, so if you do choose to use it, exercise extra precautions. Also keep in mind that the general public (particularly in North America) has long been taught to avoid it at all costs, so it may be better for your sales to give it a skip.
Sources for lead include lead carbonate, as well as frits lead bisilicate, lead sesquisilicate, and lead monosilicate.
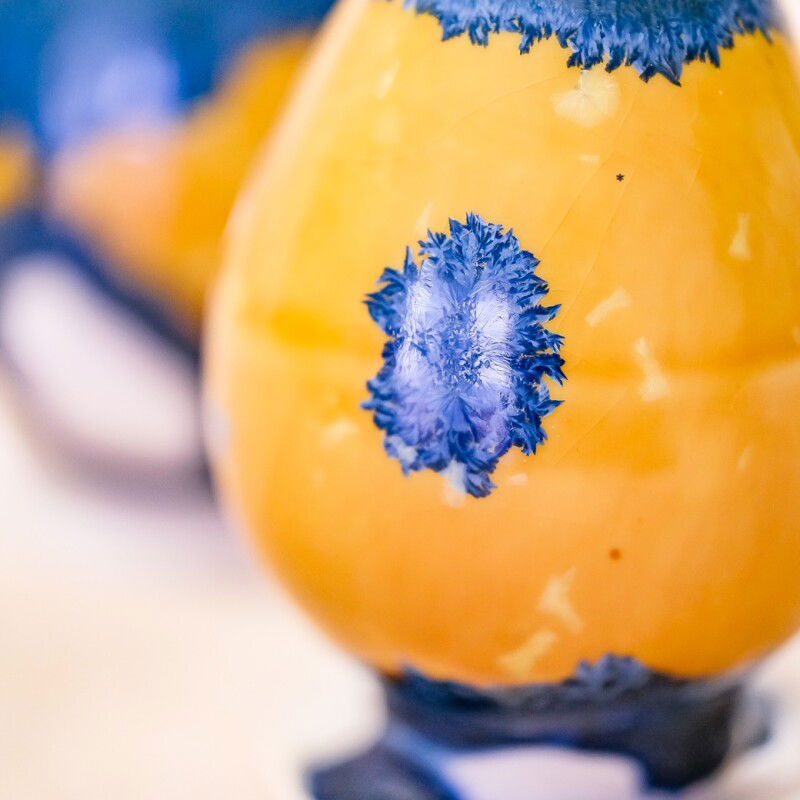
Zinc Oxide (ZnO)
Zinc is used as a flux across a broad range of temperatures. With a low starting melt at around 1832F (1000C) it can be a good substitution for lead. It can also be used to improve surface quality and durability in stoneware glazes.
It’s a powerful flux, so it is only used in small amounts. Higher amounts will result in rough surfaces. It has a low thermal expansion, so it can be used with fluxes at the other end of the spectrum to reduce the risk of crazing.
It can be used to help create greens in combination with nickel, but will interfere with the development of blues, browns, greens, and pinks, and is not recommended with copper, iron, or chrome. It has great crystal-forming properties, so is a common ingredient in crystalline glazes.
ZnO is available in pure form, as zinc oxide.
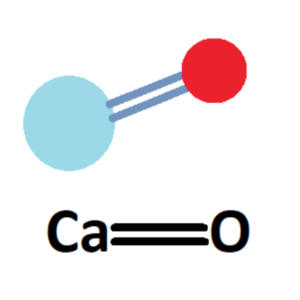
Using Some Basic Chemistry to Help You Identify Fluxes
Now that we’ve covered the main fluxes you’ll likely encounter, you may have noticed a pattern in the chemical names of these materials. All of them end in O. As we said at the beginning, they’re all oxides, and this means they have oxygen in their molecular makeup. In the case of fluxes, the oxides only carry one oxygen molecule. These are broadly described as RO (with the R standing in for the other molecule, such as calcium, or “Ca”, in the case of CaO). You may also see R2O ingredients, such as with K2O (potassium oxide), where there are two of the non-oxygen molecules but still only one oxygen.
Other materials we use, such as the silica we talked about last week, also end in O, but with a 2 after (SiO2), meaning they have 2 oxygens (dioxide), or RO2. You’ll also come across R2O3, which will come up next week.
So, if you see a glaze ingredient that is an RO or an R2O, chances are it’s a flux, even in cases where it’s primarily used as a colorant!
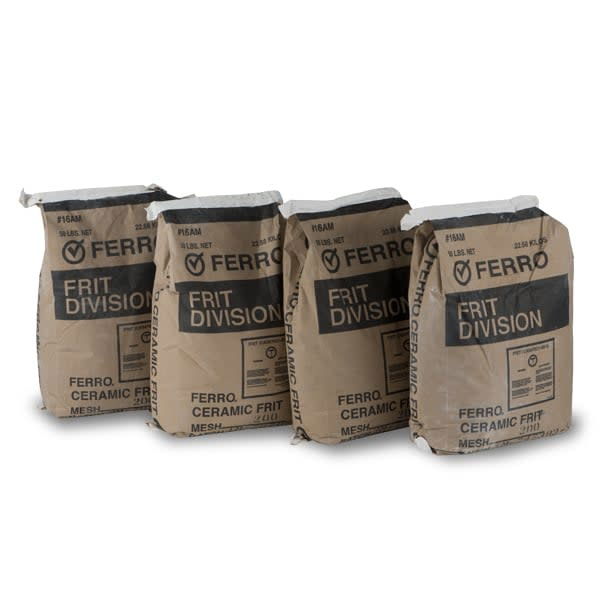
/ferro-frit-3124-out-of-stock.html
More About Frits
As you remember, we mentioned in our previous article that frits, while providing some silica, are primarily used as fluxes. You’ll have also noticed that almost all of our oxides above are also available as frits. But what exactly are frits, and why would we choose to use them?
Unlike ingredients such as soda ash, or calcium carbonate, which are naturally occurring, frits are manufactured. They’re made by melting mixes of raw materials in special kilns, then pouring the molten mix into water, and finally grinding it into a fine powder. This process has a lot of benefits over traditional raw materials, primarily because it allows the different particles to melt in unison, which does not happen with mixes of raw materials.
Because of this unified melt, frits generally produce an overall better melt with fewer problems, such as microbubbles. They also form a better interface with the clay (meaning the glaze more strongly adheres to the clay body). And finally, they are much more predictable than raw materials, providing more consistent results.
The main downside of frits is that they are much more expensive than traditional materials, precisely because they are a manufactured product. While this may put you off, be sure to consider the value of highly consistent results with fewer defects. It may just be worth the cost!
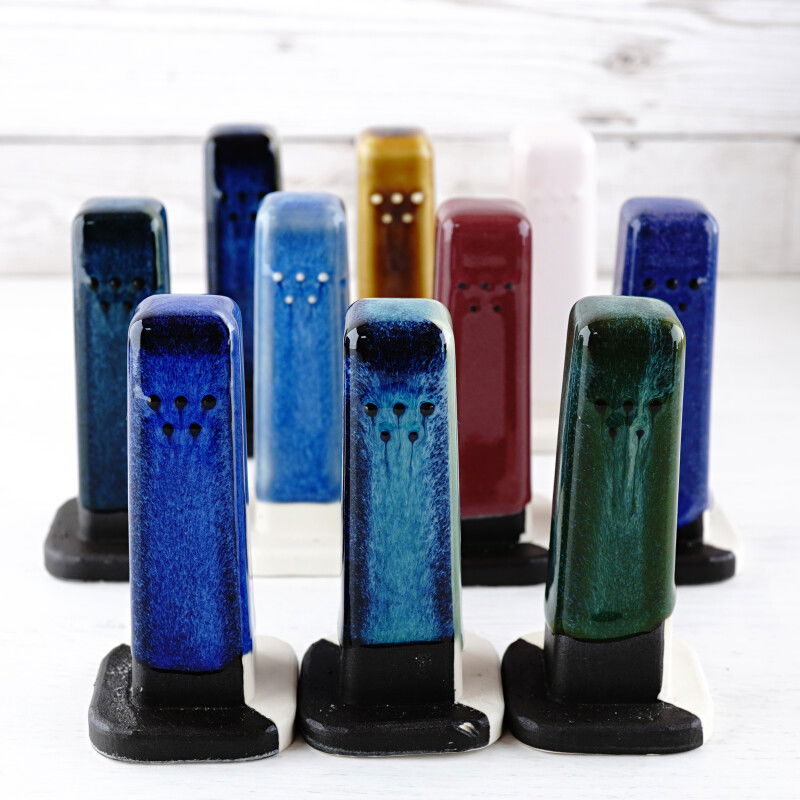
with a base recipe primarily sourcing the flux from CaO
Understanding ceramic fluxes is a key step in building your glaze knowledge, and is instrumental in your path to developing your own glazes. Whether you’re using raw flux materials like feldspars or zinc, or experimenting with frits, the interplay between fluxes, glass-formers, and refractories is what shapes the final outcome of your pieces.
We’re glad you’ve joined us today for Part 2 of this series, and we hope to see you again for Part 3, where we’ll take a look at the third integral glaze component: Refractories. If you missed Part 1 on glass-formers, be sure to check it out here.
If you are ready for a true glaze deep-drive, why not sign up for Karen Kotze’s workshop “Building your own Extensive Glaze Library”? Karen will not only teach you essential glaze chemistry, but will also walk you through the cost, sourcing, and storage considerations!
Responses