Many potters fear glaze development…
Especially with regards to:
– The chemistry and maths behind it
– Sourcing materials which is sometimes hard to come by in certain countries
– The additional space taken up in the studio for such a venture
– And of course the cost – knowing that you would probably have to do hundreds of tests before you have glazes that tick all the boxes – like a good melt, easy to work with etc.
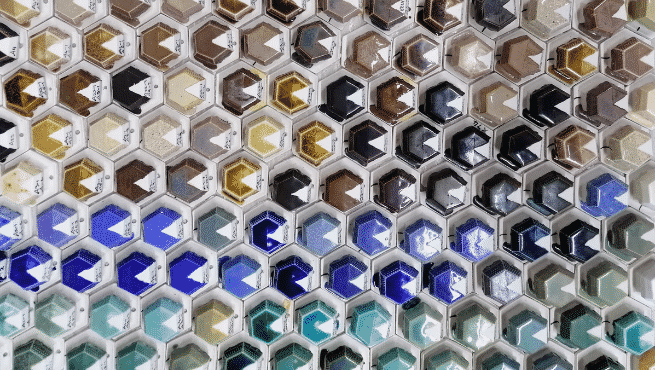
With this tutorial I will show how I overcame all of these points
- No understanding or studying of chemistry is needed
- By using a simple system, you don’t have to keep track of percentages throughout the whole process
- All you need is your favourite ready-made transparent glaze that you can buy from your local pottery supplier, and then 9 other basic ceramic raw materials that have been used for centuries.
- Due to the small amount of material used you need very limited space to do this. My studio in 23m2 and I do this glaze development, mould making, slip casting (sometimes of 500 or more pieces per order) and handbuilding.
- No material goes to waste. Your raw materials should be available in 1kg or smaller supplies and reasonable prices, therefore you do not have to lay out huge amounts of money to develop your own extensive glaze library.
Basically, I’m going to show you how to make amazing and unique glazes by systematically working through lots of possible combinations.
Accept and embrace the 1000s of options that you will be able to make. Don’t get stuck on trying to copy what you have already seen.
I have done 90% of my own development with a wide firing midrange (cone 6) transparent glaze that I get from a local South African supplier.
To date I have not been able to get any indication what the molecular makeup of this glaze is. It has, however, given me amazing results and a truly wide firing. Even down to cone 3 with small amounts of added flux.
I can’t guarantee the same result for the glaze that you will be using…
But it sure won’t cost you a lot to give it a try.
Just on a last note.
I often get the question “Why would I want such a huge library of glazes?”
Well, I do some site specific wall installation like this commission:
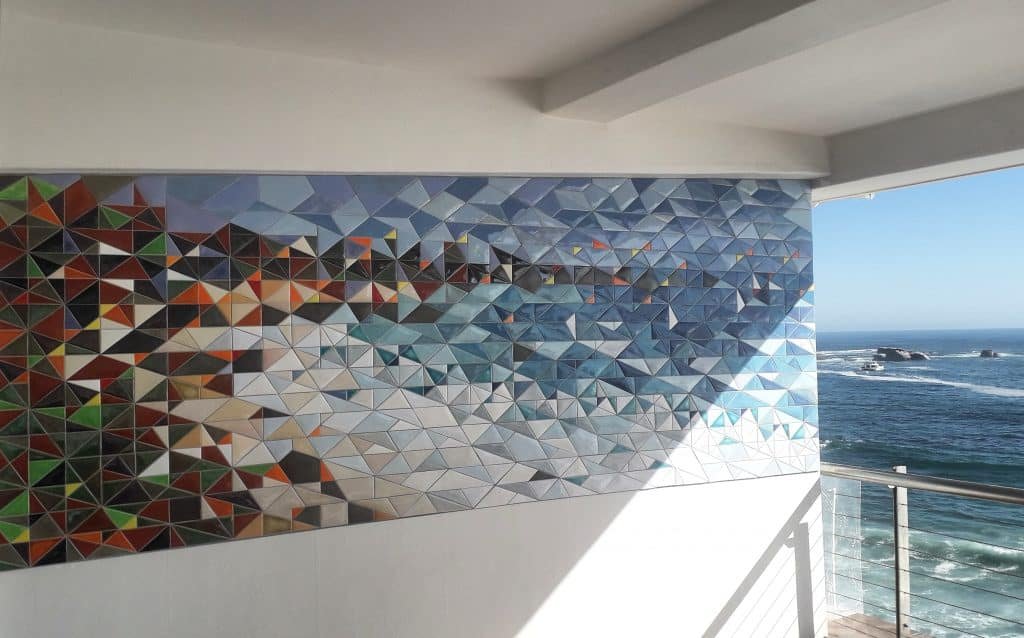
Rolling Tides Commission
And I need glazes like a painter would need coloured paint.
In addition, I could add some special qualities to these tiles that resonate with its representational counterpart in the landscape.
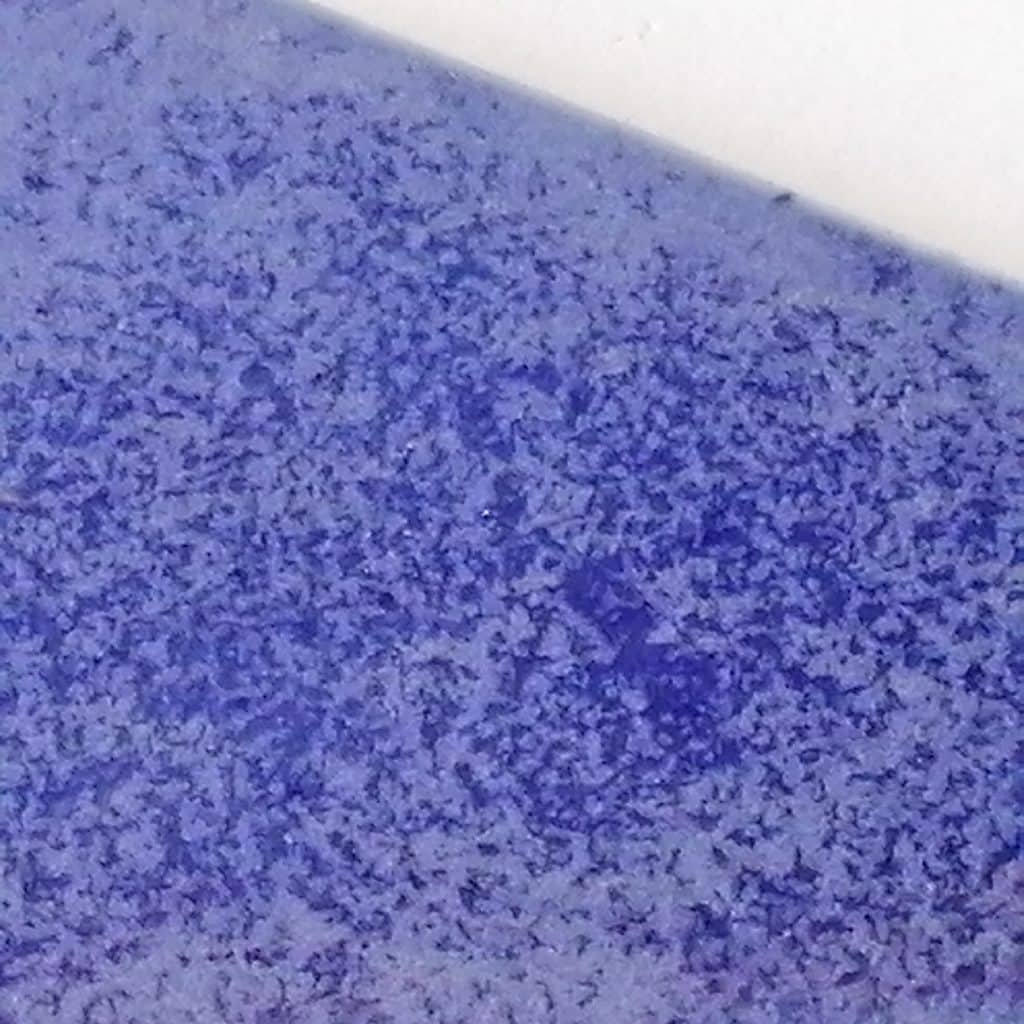
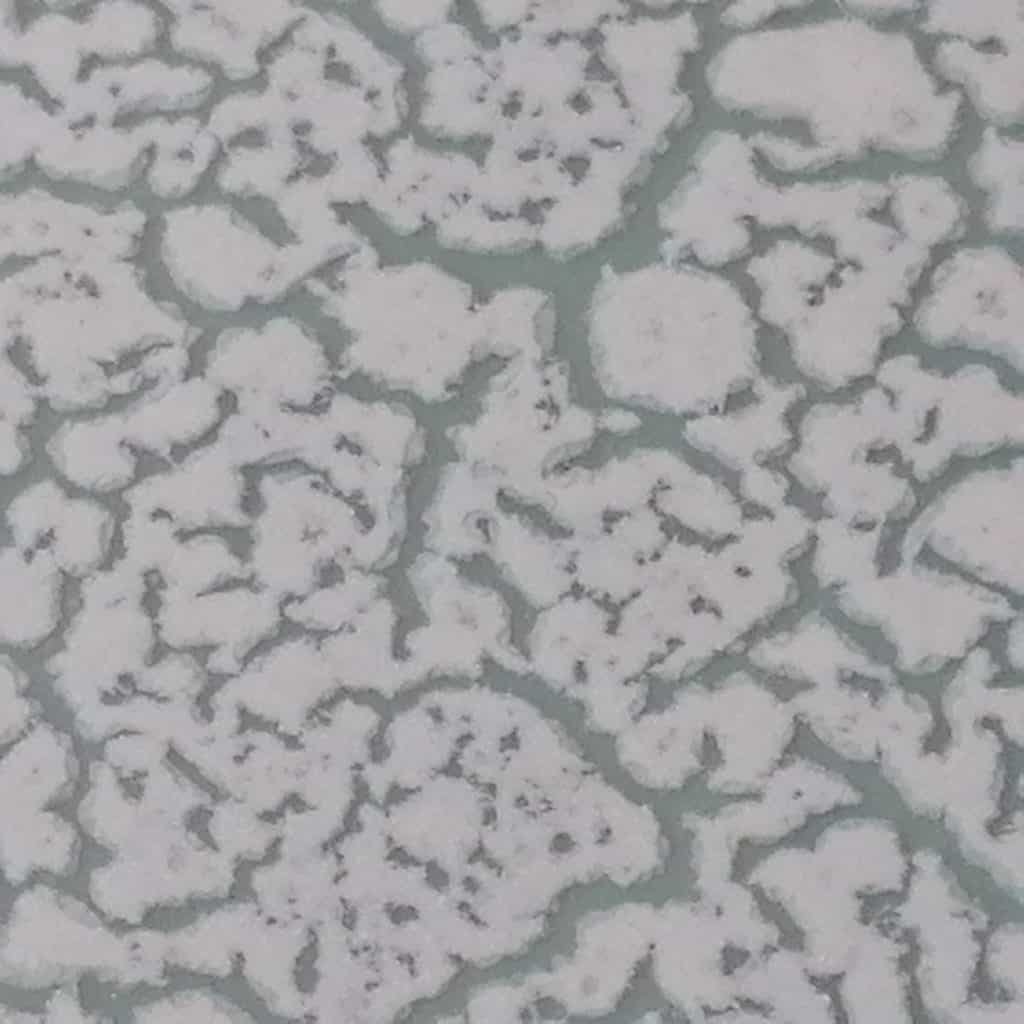
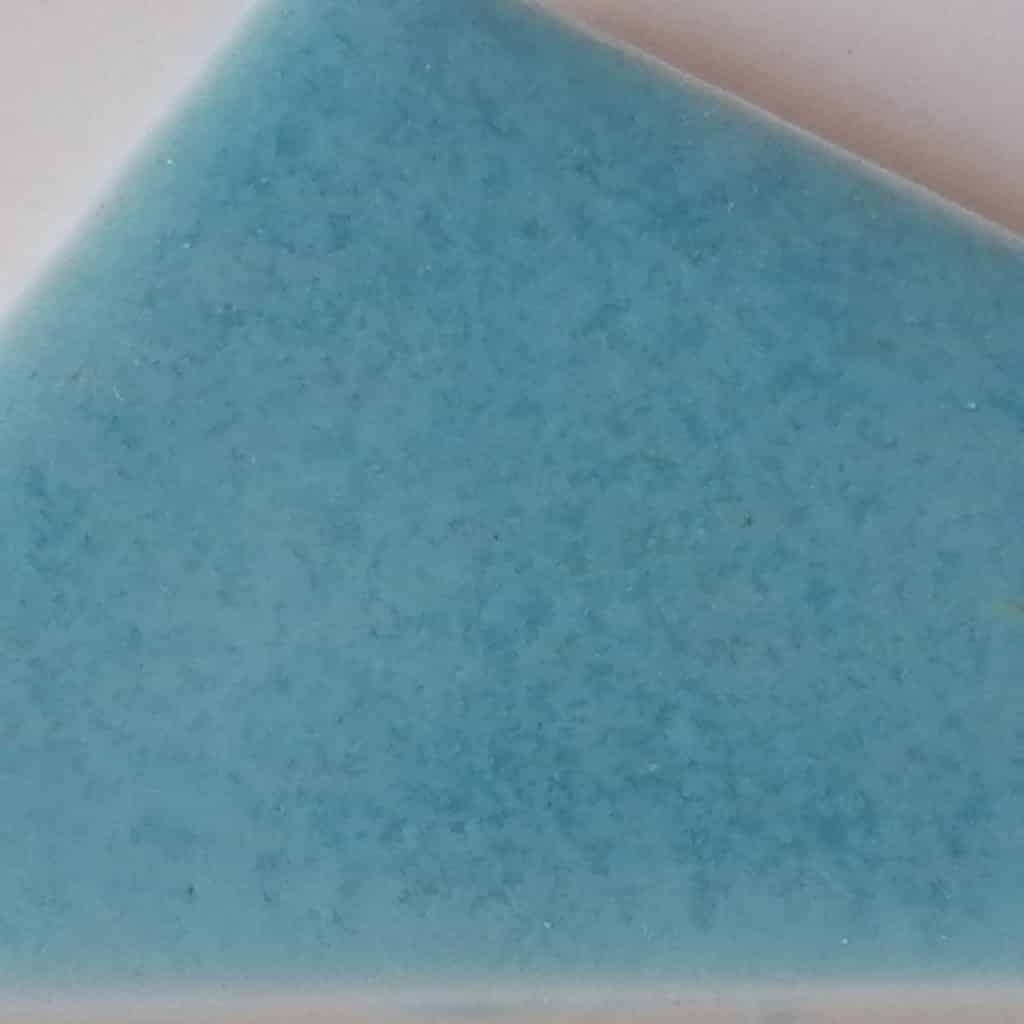
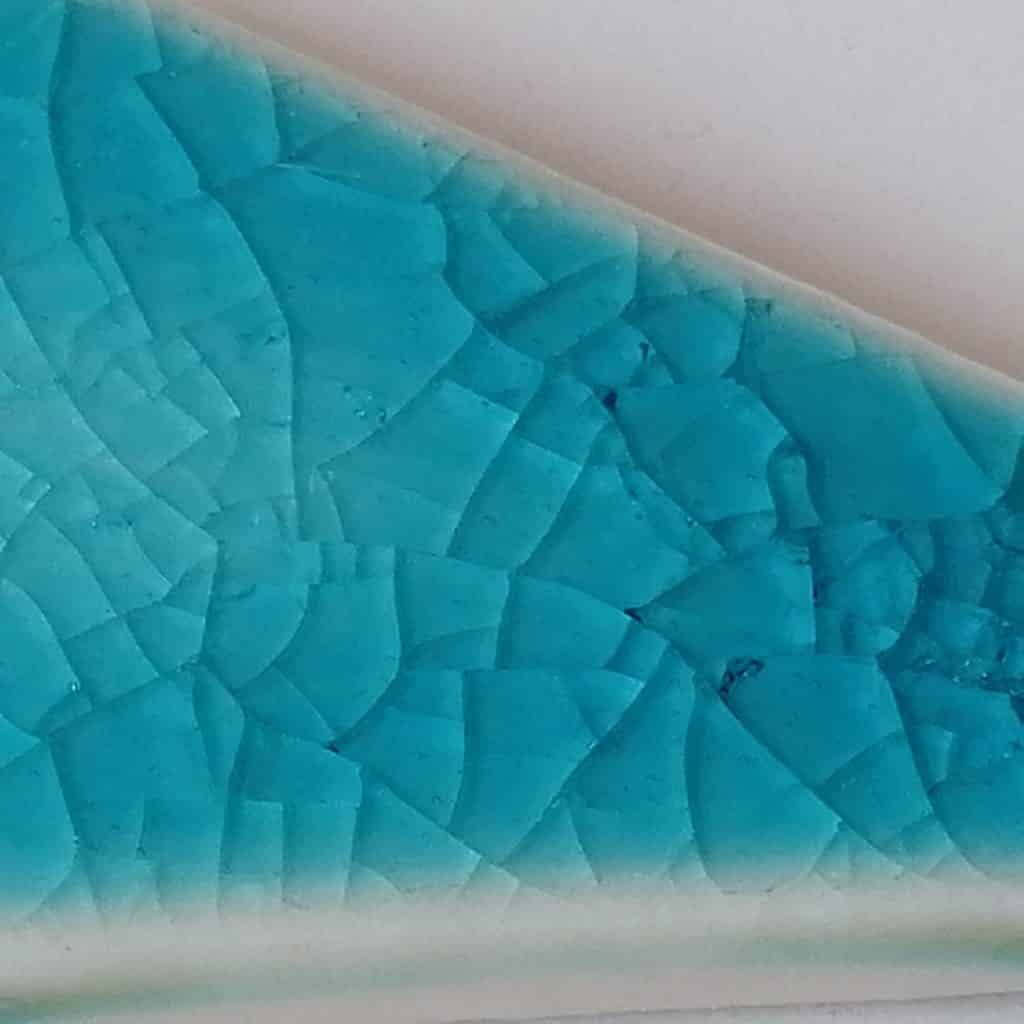
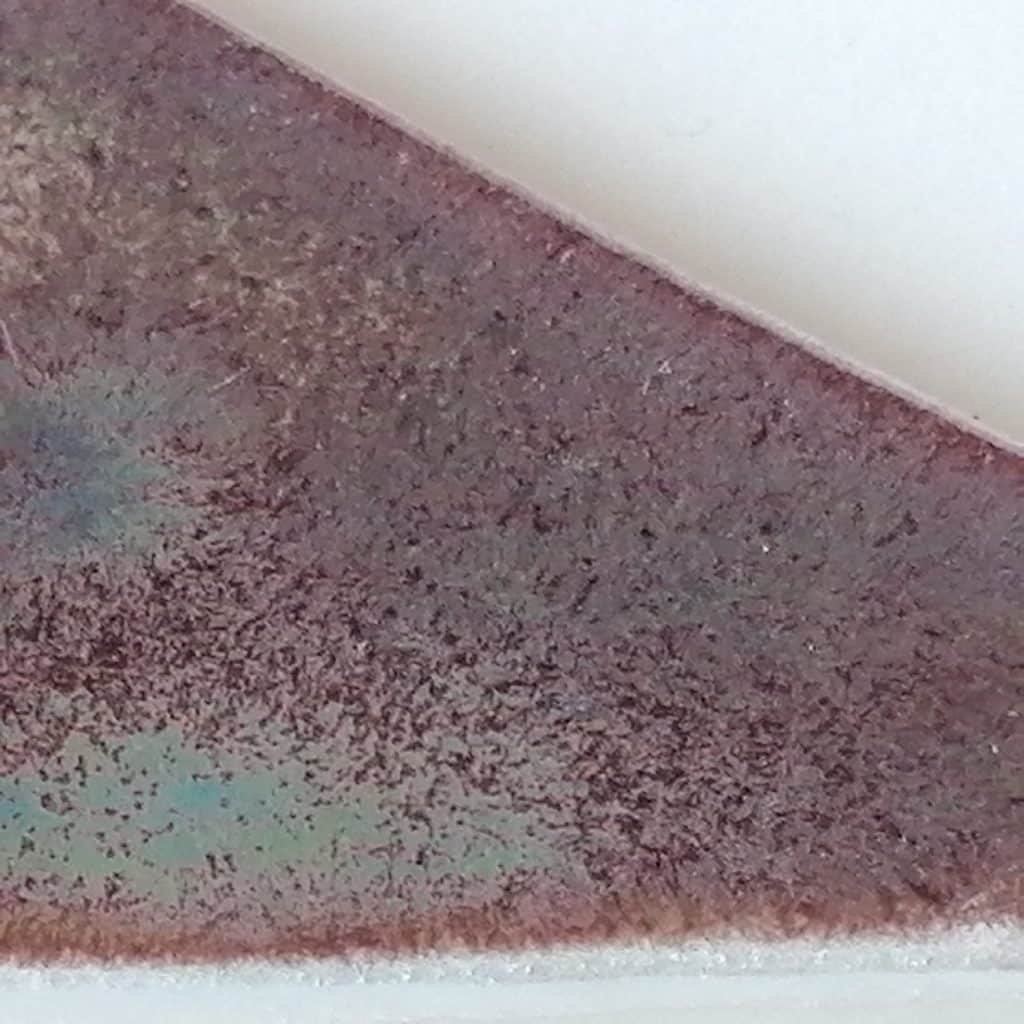
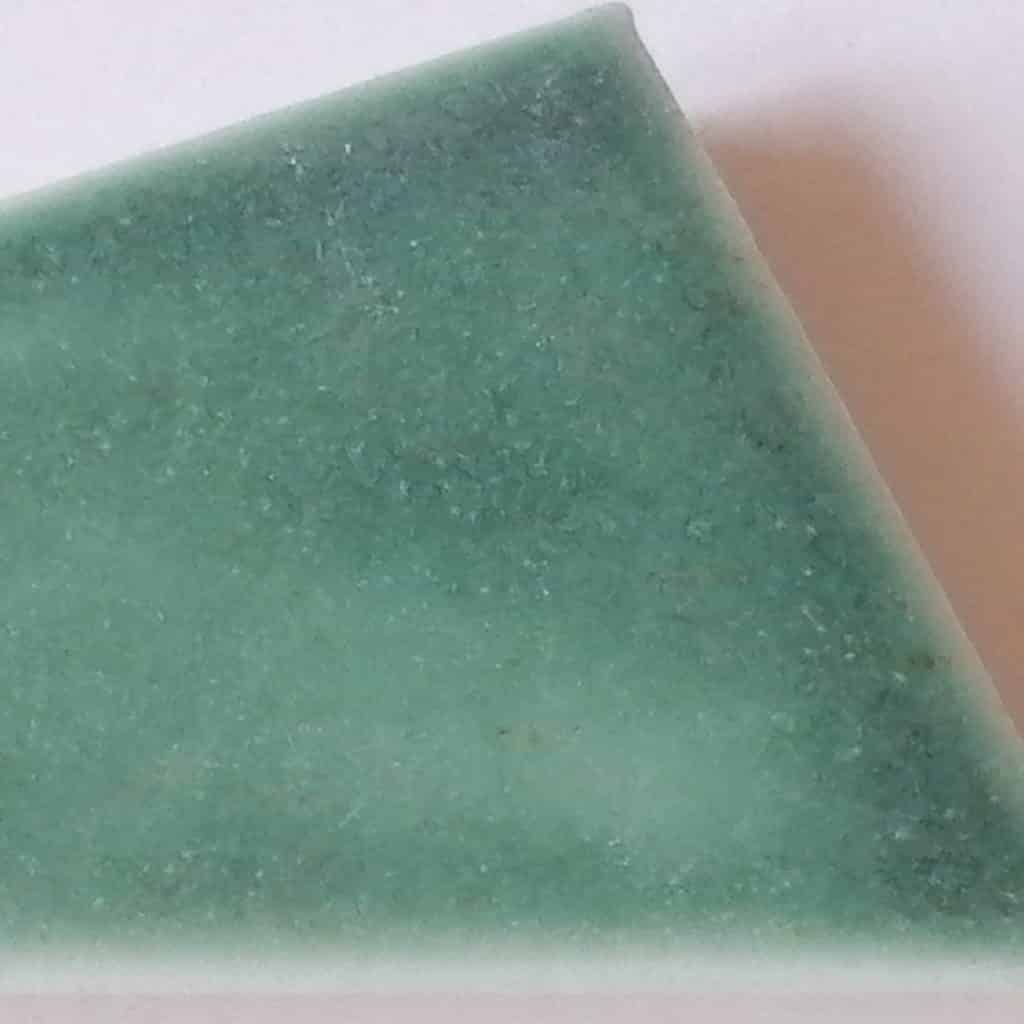

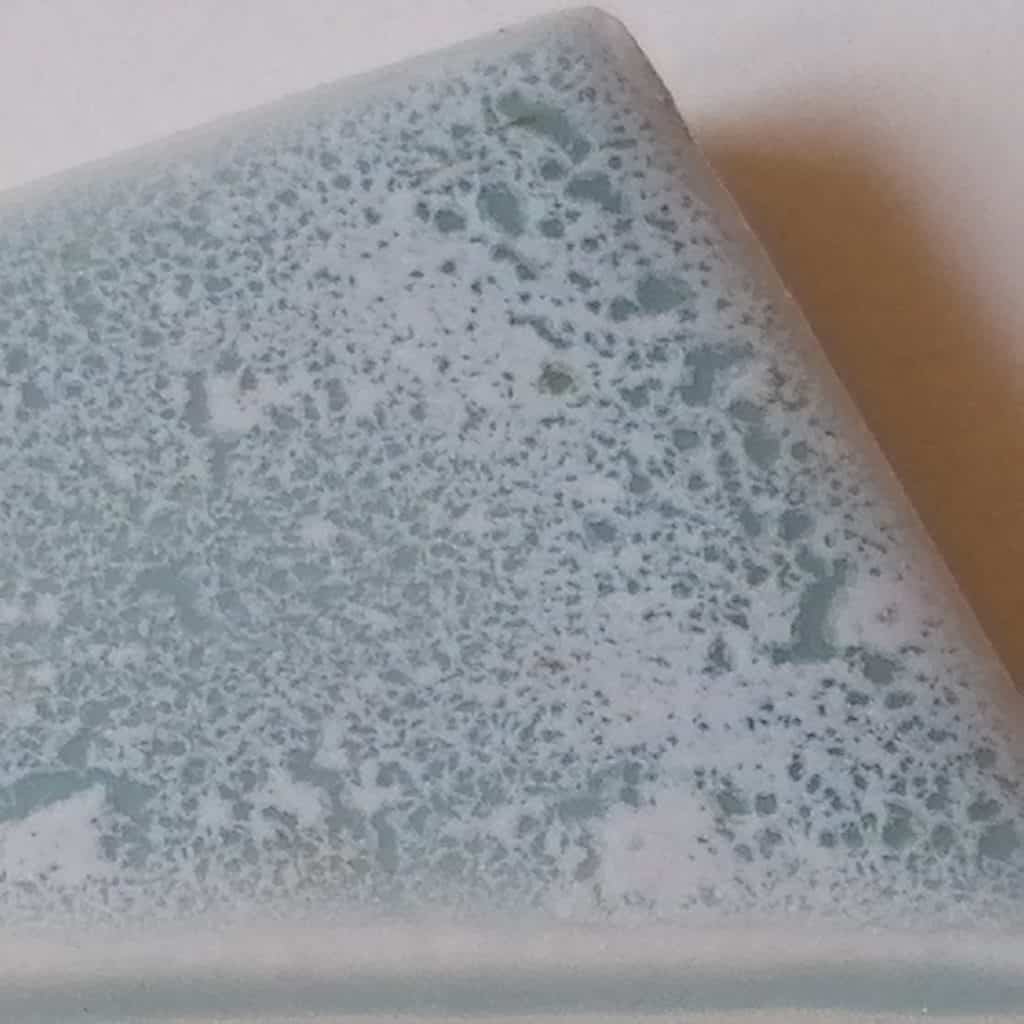
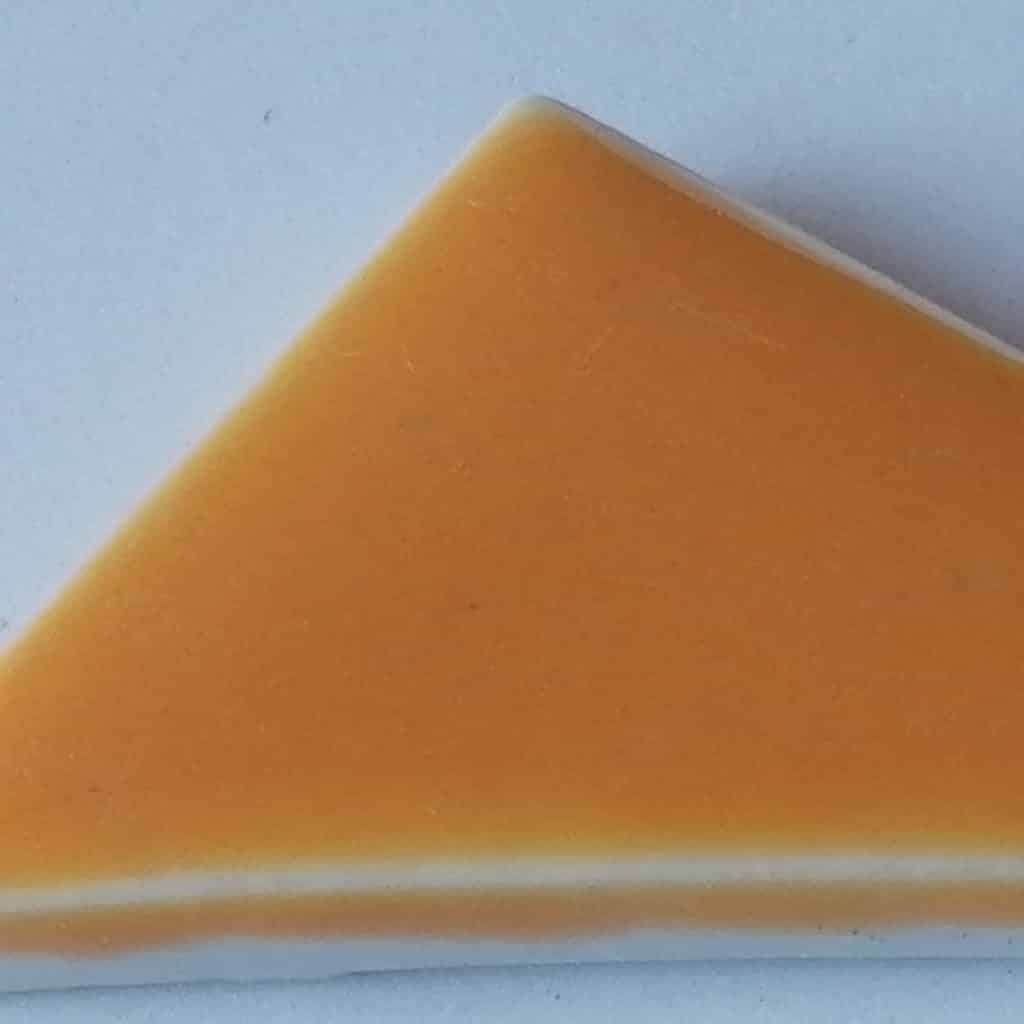
I also do lots of specific item development for companies or individuals that would like to launch unique and limited quantity bespoke ranges, and it is great to give them so much option to choose from, in order to suit the design feel.
These are materials needed:
- 2kg of your preferred base glaze (giving a good melt at cone 3 to 6 range)
- 10g Cobalt Oxide
- 40g copper Oxide
- 40g Red Iron Oxide
- 40g Manganese Dioxide
- 20g Nickel Oxide
- 40g Zircon
- 40g Tin Oxide
- 40g Rutile
- 40g Lithium Carbonated
- 40g Magnesite
- 40g CMC gum
Equipment:
- Scale accurate to 0,0g
- Glaze sieve
- Hog hair brush
- 10 small plastic containers
- 10 250 ml plastic containers with lids that seal really well.
- 5 small soft paint brushes
- Ceramic marker I use this applicator with underglaze
- Test tiles
- An oven to dehydrate glaze mixtures.
- I will also give you a Triaxial blend map (available in the resources)
When you purchase this workshop, you get my Workshop Videos:
Instant Access to watch my workshop videos. 4 parts, totaling around 4 hours of video.
You get my Equipment List PDF
Watch my Q&A
Watch my Q&A where I answered questions about my process.
You Get Lifetime Access to the Replays
The workshop Q&A will be recorded, and you will have lifetime access to it. You can watch it online, or download it to your device to watch offline at any time.
About Karen Kotze
The ceramic process is such an intriguing but challenging process for me. It is a multi dimensional field and I have spent the last 20 year exploring various focus fields in depth.
I started with handbuilding, creating intricately woven plates in earthenware and porcelain that was purely decorative in nature. I then moved onto slab building functional ceramic vessels from porcelain. I progressed further when I started making my own moulds with the help of 3d printing technology in order to slip cast. The final in depth field I am currently immersed in, is glaze development. But glaze development with a slightly different approach than usual.
Through the years I realized that I find a deep satisfaction in refining a process and workflow in the ceramic medium in whichever field of ceramics I might find myself in at that stage. The final result of my efforts is almost not as important to me as organizational, problem solving and systamition of the process: in order to render every step of the process and enjoyable and efficient as possible.
Web: www.wovenceramics.com
Instagram: @wovenceramics