Whether you’re working with commercial glazes or looking to start mixing or developing your own, understanding the basic structure of glazes can be a big help in getting successful results. It’s easy to get overwhelmed by the sheer number of possible ingredients and complicated recipes, but you don’t need a chemistry degree to improve your understanding.
In this new series, we’re going to cover the three essential components that all glazes have: fluxes, glass-formers, and stabilizers. We’ll look at what they do, how they work together, and which ingredients can provide them. And later in the series, we’ll look at the most common additions to glazes: opacifiers and colorants.
By breaking your glazes down into these basic categories, you’ll have a better understanding of how your ingredients are contributing to your glaze, and which ones to adjust to get your desired results. It will also help you make substitutions if you suddenly lose access to a particular material.
We’re going to start off our glaze journey today with the foundational element of most any glaze: the glass-former.
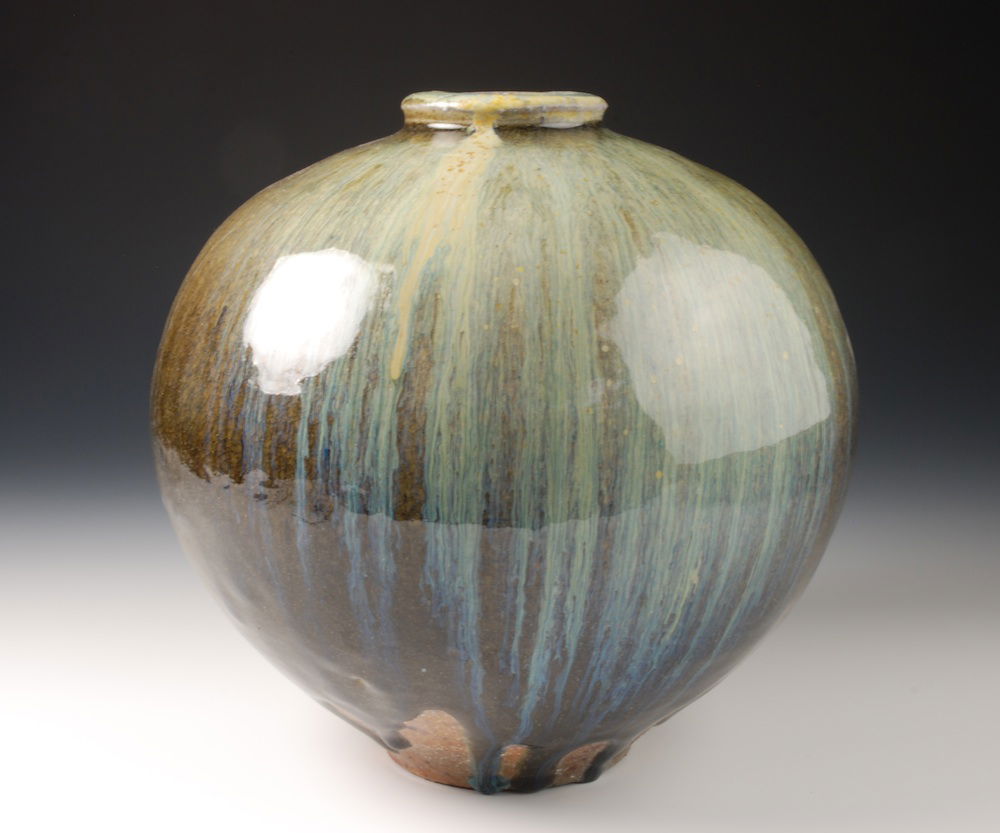
featuring a high-gloss glaze
Why do Glazes Need a Glass-Former?
Now, you’ve probably already noticed that most glazes, especially glossy ones, have a glass-like feel. That’s no coincidence, since glaze, at its core, is a skin of glass. Glazes were originally developed to make pots more water-tight and strong, and glass is the perfect material to do this. It’s hard and dense, with little porosity.
Since we are applying the glaze to a three-dimensional object, we need to source our glass-former in a powdered form which can be suspended in water. Later, we’ll use the heat of the kiln to melt it and fuse it to our work.
Where Do We Source Glass-Formers?
Glass is formed essentially by one ingredient: silica, or more accurately silicon dioxide (SiO2). You’ve likely already noticed it is a common ingredient in glaze recipes. It’s a foundational component of glass, and is found in common materials such as sand, limestone, mica, and many others. For the purposes of glazing, we can source silica from a number of materials. Let’s have a look at a few of them below.
Quartz/Flint/Silica
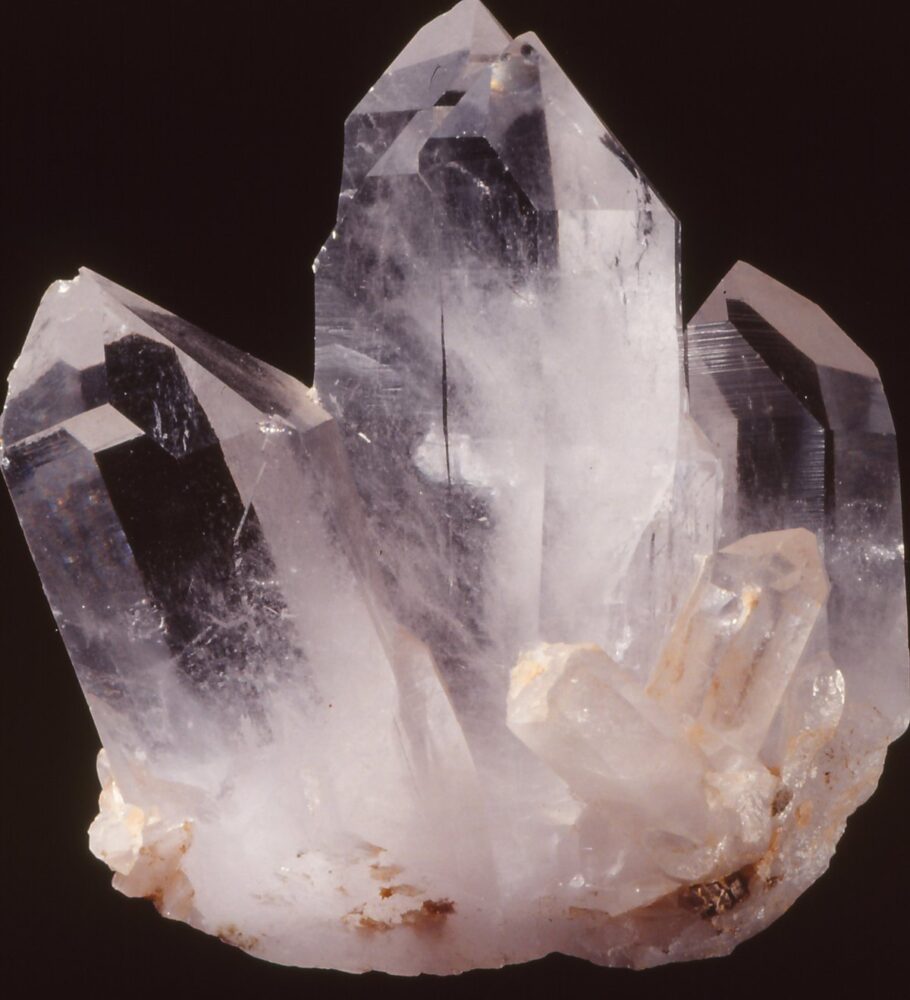
Quartz is a near-pure form of silica that is naturally forming, and you’ll likely see it as the main source of silica in many glazes. It is formed in igneous or metamorphic rocks as silica cools over long periods of time, a process which forms large angular crystals. Quartz has a very high melting point and a high rate of thermal expansion.
You’ll often see the terms quartz, flint, and silica used interchangeably in recipes and at your pottery supply store, and this can create some confusion. By definition, flint is different from quartz, being a finer particle found in sedimentary rocks. True flint is very high in silica (at about 94%), but it does contain more inclusions of other minerals than quartz. It has been used in glazes, but is actually not commonly used in glazes today. The ‘flint’ you’re seeing in your glaze recipe today is actually ground quartz, and, since it is no longer in its crystalline form, it is most accurately called silica.
You may come across different “meshes” of silica, such as Silica 200 or Silica 325. This refers to the particle size of the material. The larger the number, the finer the particle. Generally speaking, finer grades melt slightly earlier, but in most cases it won’t make a significant difference in your glaze.
Because it melts at a high temperature, you will often see low amounts of silica in earthenware glazes, but as much as 30% in glazes for high firing stonewares.
Wollastonite
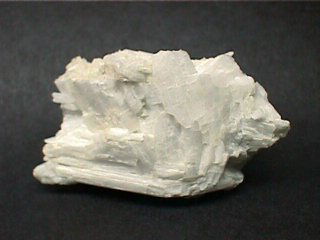
This is calcium silicate, so you can see the presence of silica in the name itself. It consists of 51.72% silica and is a naturally occurring white mineral. This material is primarily used for its calcium content, which is a powerful flux (we’ll cover fluxes in Part 2), but it’s important to be aware of the amount of silica it’s contributing to your glaze.
Kaolin
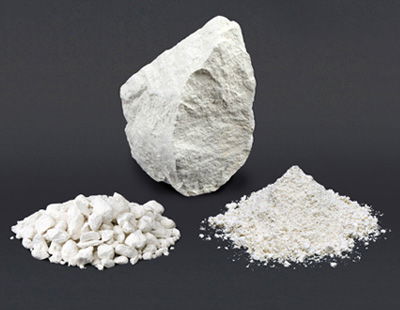
Probably better known for its role in porcelain clay, kaolin is also a common glaze ingredient. It contains both silica (it’s made of up to 47.29% of it), and alumina oxide, which is a stabilizer (we’ll cover this in Part 3). While contributing silica itself, kaolin is most commonly used to prevent your main source of silica from settling out in your mixture.
Feldspars
Feldspars are practically full glazes in and of themselves, containing silica, refractories, and fluxes. The feldspar powders that we use in ceramics are made from crushed crystalline rock containing a mixture of aluminum silicates of sodium and potassium, and smaller amounts of other minerals. Feldspars can be composed of up to 65% silica, though they are more commonly used for their fluxing properties. Fun fact: feldspar is the most common mineral type on Earth, with quartz being second!
Bentonite
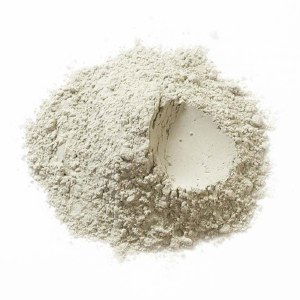
Also containing 59.00% silica, bentonite is usually only added to glazes in small amounts (1-2%), so it’s not going to add too much silica to your glaze. Its main use is to prevent your glaze from settling out. It is a clay-based material with a very high degree of plasticity.
Ball Clays
Ball clays are fine, plastic clays that are formed by the deposition of clay minerals and volcanic ash. They contains kaolinite, quartz, mica, titanium, iron, and small amounts of feldspars, bentonite, and illite. Ball clay also tends to contain varying amounts of organic matter. They can contain up to 59.00% silica, but are typically employed in glazes to help suspend and harden them, and control their shrinkage during drying.
Frits
Frit is another ingredient that is primarily used for its fluxing properties. Frits are manufactured materials that primarily consist of ground glass. We’ll go into a lot more detail about frits in our next article, but be sure to keep the silica content of them in mind when you are adding them to your glaze. As they are manufactured, there are numerous different ones available, each with a differing percentage of silica.
We hope that today’s article has helped demystify one of the core components of glaze composition: the glass-former. From its vital role in creating smooth glassy surfaces, to understanding what ingredients provide it, you now have a better understanding of this fascinating material. Be sure to join us in Part 2 of this series, where we’ll delve into the importance of fluxes.
If you would like to learn more about glazes and their chemistry, be sure to check out our selection of glaze workshops! Why not sign up for Greg Daly’s “Developing Glaze Surfaces” or Matthew Blakely’s “Making Glazes from Rocks, Clays, and Ash.”? No matter what your level of glazing experience, we have a workshop perfect for you!
Responses
This is great information. Could I have it on a PDF format so I can download?